NdFeB Magnet Machining and Electroplating Process
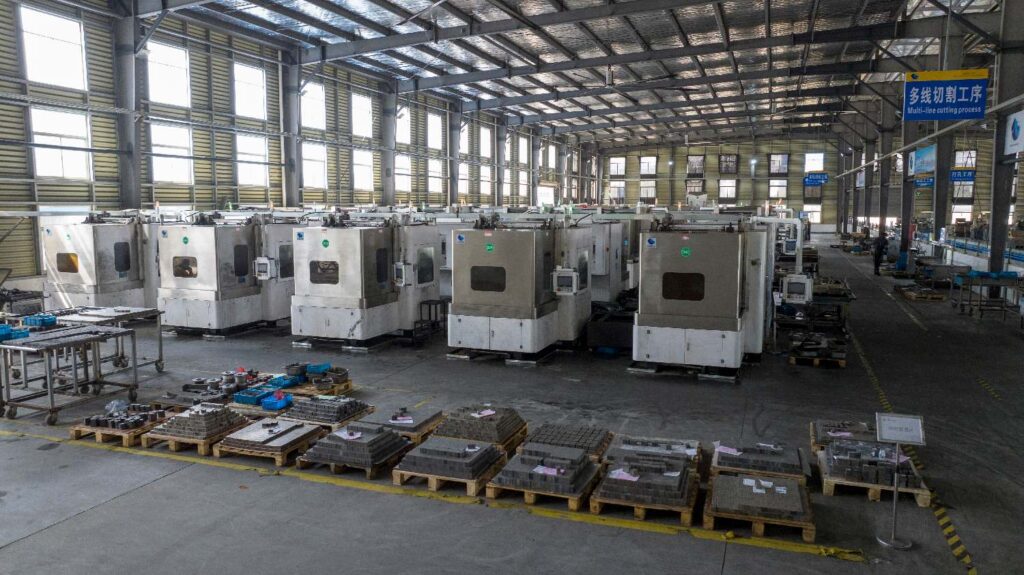
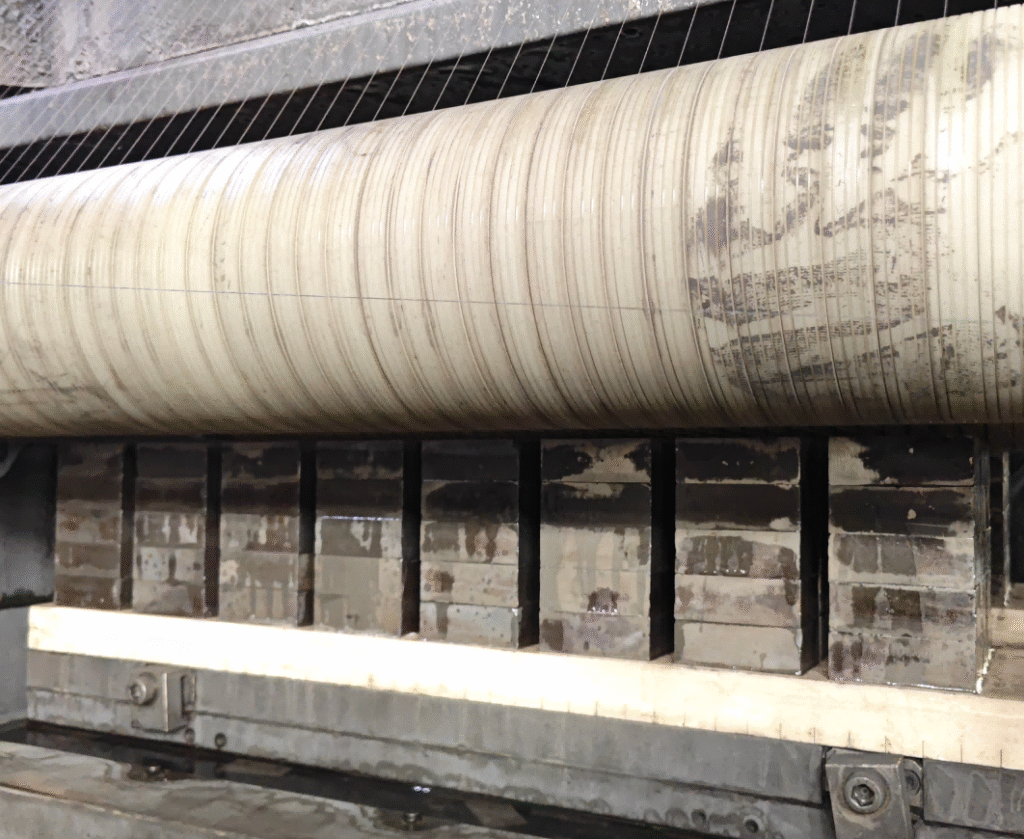
NdFeB Multi-Wire Cutting and Grinding Process
Multi-wire cutting serves as the core process for mass production of NdFeB magnets. Utilizing diamond wire saws enables high-efficiency cutting with processing speeds reaching 20-30mm/min, making it particularly suitable for large-scale production. By optimizing wire diameter (0.12-0.18mm) and slurry formulation, the process achieves ±0.05mm precision while maintaining material loss below 5%. This method allows simultaneous cutting of hundreds of blanks, significantly improving production efficiency. For grinding operations, different processes are selected according to product geometry: double-sided grinding for sheet magnets requiring high parallelism, vertical grinding for irregular shapes, and centerless grinding specifically for high-precision cylindrical magnets. Through combined use of diamond grinding wheels with various grit sizes (200-1000 mesh), surface roughness of Ra0.4-0.8μm can be achieved to meet diverse application requirements.
NdFeB Electroplating Protection Process
Electroplating is essential for NdFeB magnets due to: 1) Corrosion protection: Neodymium’s high chemical reactivity makes it prone to oxidation, where plating layers provide environmental isolation; 2) Mechanical enhancement: Coatings improve surface hardness and wear resistance; 3) Operational safety: Preventing magnet fragmentation. Multiple options are available based on application environments: Zinc plating offers low cost but basic protection for ordinary conditions; Ni-Cu-Ni multilayer coating provides better corrosion resistance, meeting 48-hour salt spray test requirements; Black epoxy resin coating delivers superior corrosion protection (up to 500-hour salt spray test) while improving appearance. For high-performance applications, composite solutions like Ni-Cu-Ni plating combined with epoxy resin coating can be employed for dual protection. These processes ensure 5-10 years service life while strictly controlling magnetic performance loss within 5%.
