NdFeB Magnet Melting Process
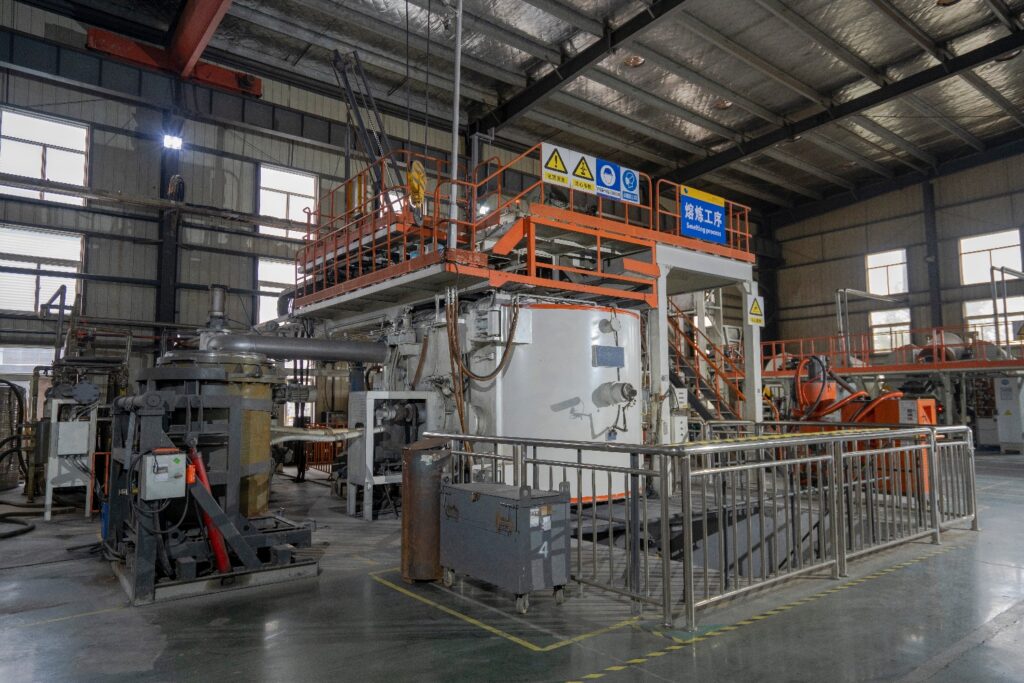
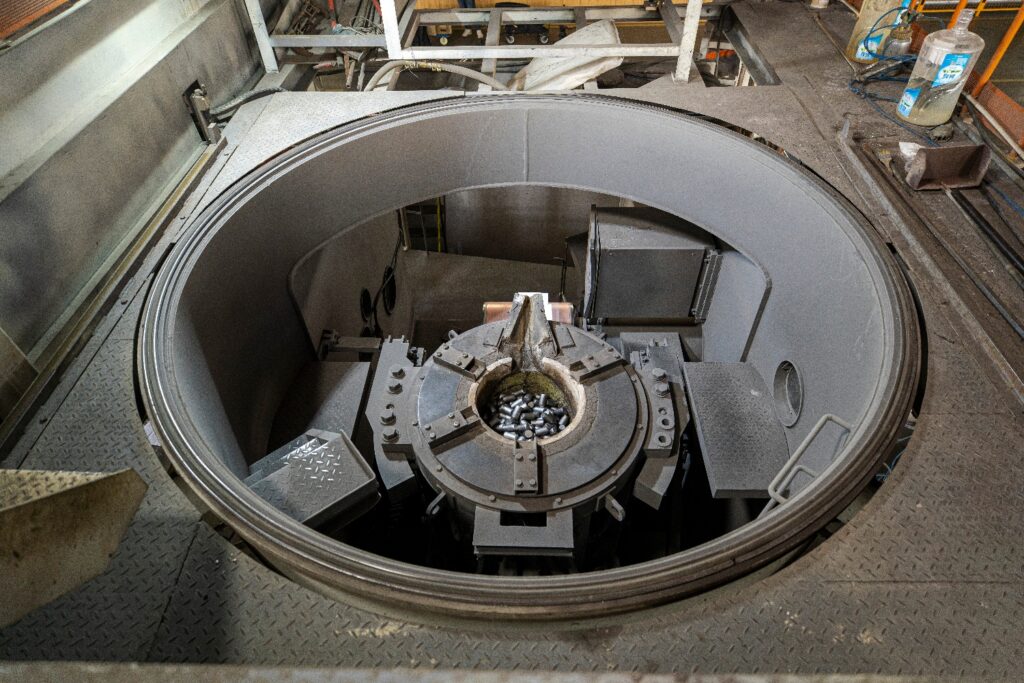
Precise Formulation of NdFeB Alloy
The performance of NdFeB alloys relies heavily on precise composition control of the main Nd₂Fe₁₄B phase. Insufficient neodymium (Nd) weakens magnetic properties, while excess Nd forms non-magnetic grain boundary phases, reducing coercivity. Boron (B) must be carefully balanced to ensure proper phase formation, and iron (Fe) content directly affects saturation magnetization. Even minor deviations or impurities can significantly degrade performance.
To optimize magnetic properties, alloying elements and strict processing controls are essential. Dysprosium (Dy) and terbium (Tb) enhance coercivity by substituting into the Nd₂Fe₁₄B lattice, while cobalt (Co) improves thermal stability by raising the Curie temperature. Aluminum (Al) and copper (Cu) refine grain structure, preventing abnormal grain growth and improving corrosion resistance. For high-precision manufacturing, raw materials must be weighed within 0.1% tolerance, often using pre-alloyed ingots to minimize segregation. Advanced techniques like strip casting ensure uniform composition before powder metallurgy. Additionally, trace elements like gallium (Ga) or niobium (Nb) can further enhance microstructure and magnetic properties. Rigorous quality control, including X-ray fluorescence (XRF) and electron microscopy, guarantees consistency in final sintered magnets. The interplay of composition, processing, and microstructure ultimately determines the performance of high-grade NdFeB alloys.
Vacuum Induction Melting and Rapid Solidification
The NdFeB alloy is melted in a vacuum induction furnace under carefully controlled conditions. After evacuating to about 0.1 Pa and backfilling with argon, the raw materials are heated to 1500-1600°C until fully liquefied. The molten alloy is then rapidly solidified by ejecting it onto a high-speed rotating copper wheel, forming thin metallic ribbons with fine microstructure.
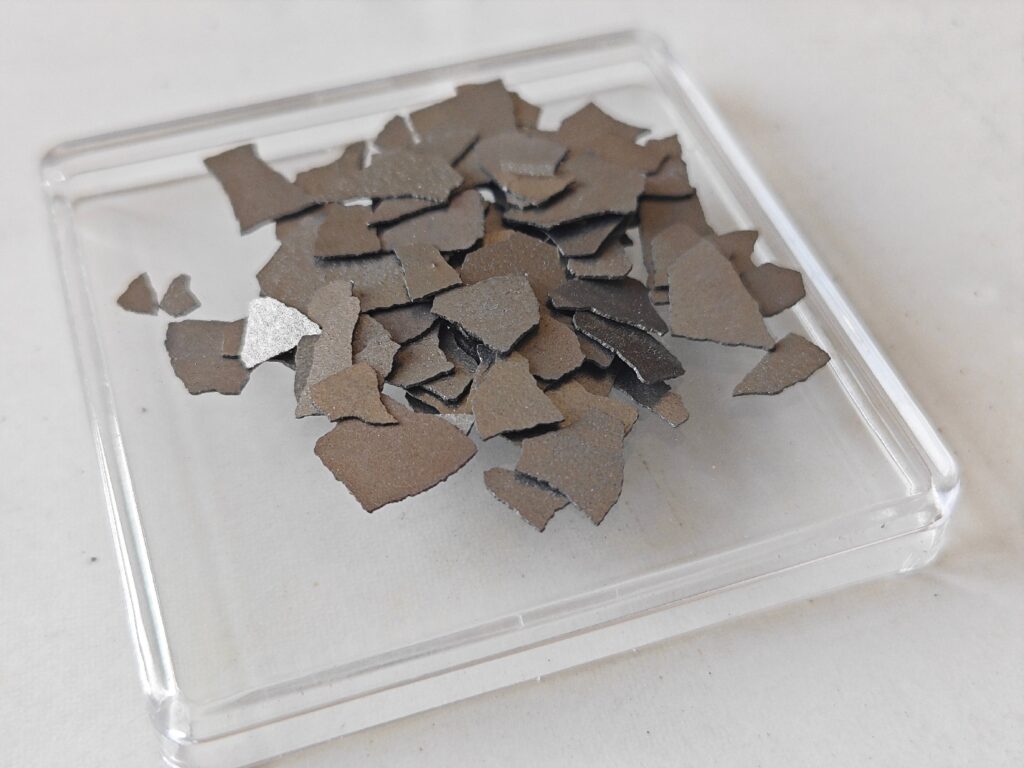
The melt-spun ribbon production process requires meticulous parameter optimization to achieve the desired material characteristics. Several critical factors must be precisely controlled:
The wheel rotation speed determines the cooling rate and significantly influences the ribbon’s microstructure
The ejection pressure affects the ribbon’s uniformity and surface quality
The melt temperature impacts the alloy’s fluidity and phase formation
The chamber atmosphere must be carefully maintained to prevent oxidation
The ultra-rapid solidification process produces ribbons with:
A nanocrystalline or amorphous structure that is ideal for subsequent processing
Effective suppression of soft magnetic phases
Controlled oxygen content to ensure final magnet performance
Brittle mechanical properties suitable for powder preparation
These high-quality ribbons serve as the perfect precursor material for the next manufacturing steps. Their uniform microstructure and optimized phase composition lay the foundation for producing NdFeB magnets with superior magnetic properties. The subsequent hydrogen decrepitation process will further transform these ribbons into the fine powder required for magnet fabrication.