NdFeB Magnet Introduction
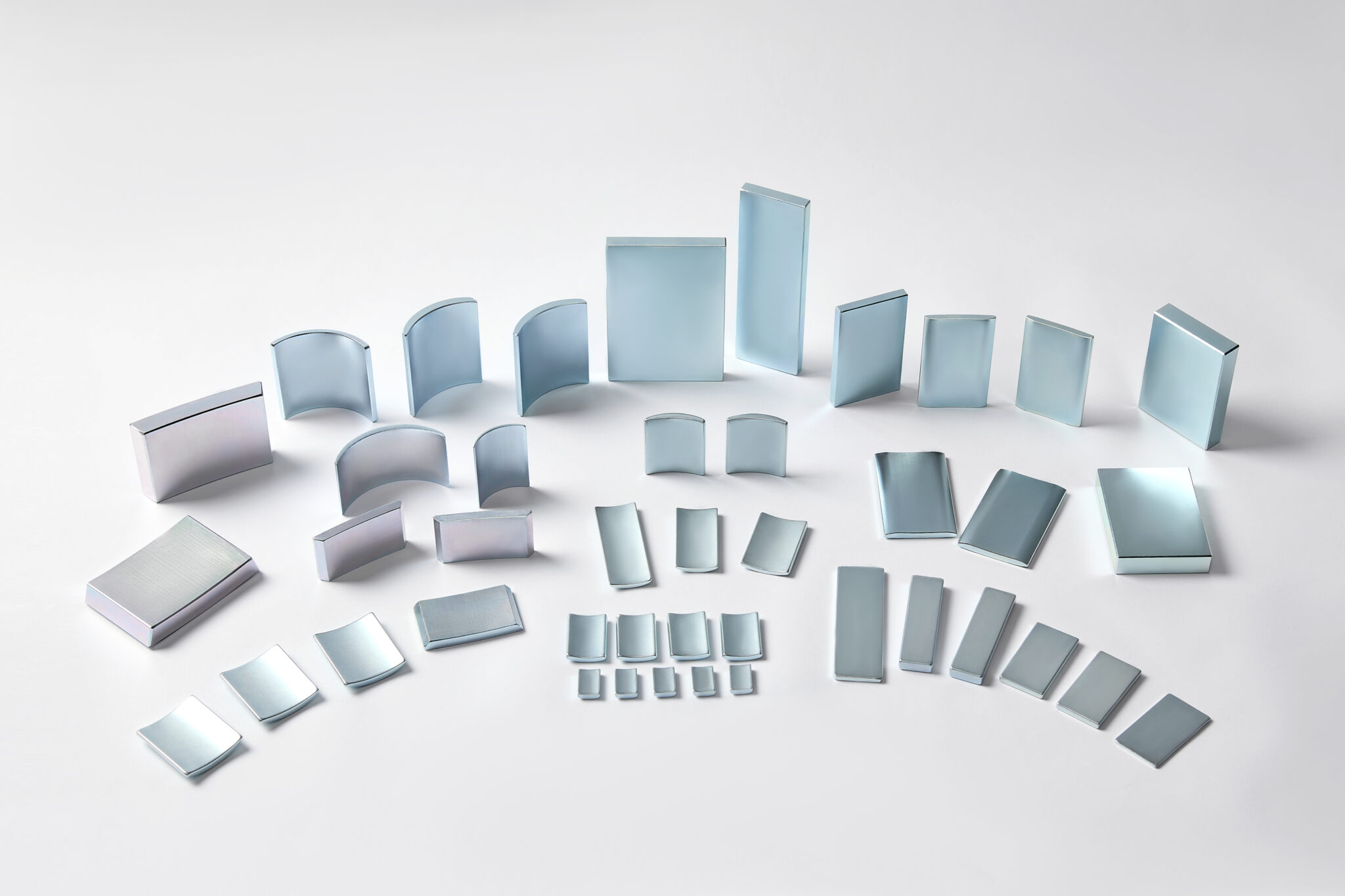
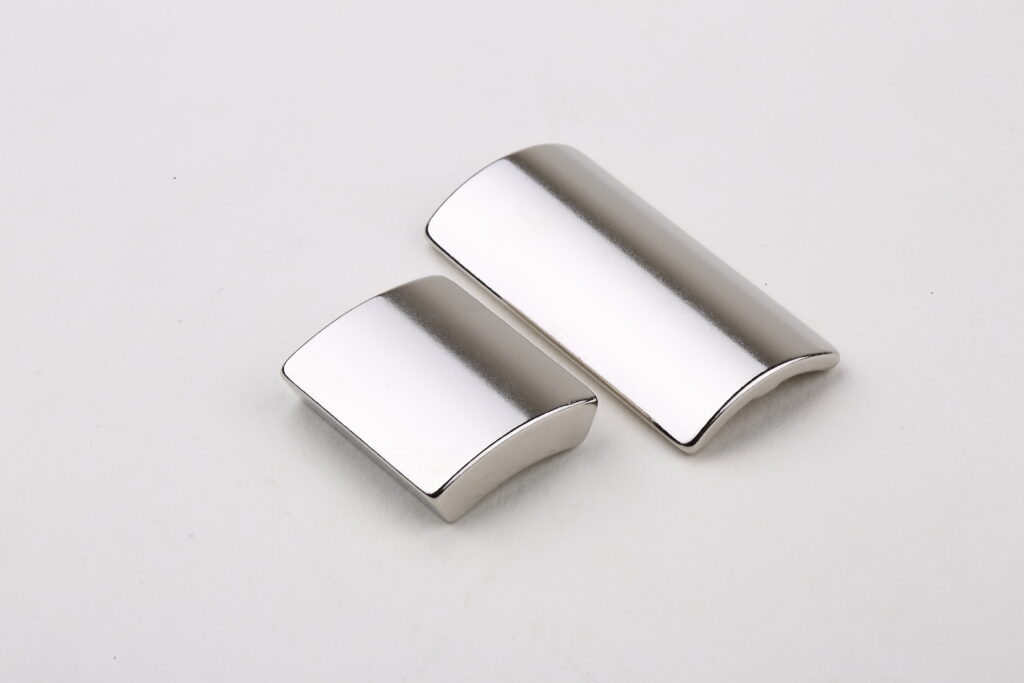
NdFeB Magnets: Redefining Magnetic Innovation
The synthesis of NdFeB (neodymium-iron-boron) magnets by Masato Sagawa in 1982 at Sumitomo Special Metals marked a revolution in permanent magnet technology. With a maximum energy product ((BH)max) of 280 kJ/m³ (35 MGOe)—three times higher than Alnico and 40% greater than SmCo₅—NdFeB magnets unlocked unprecedented possibilities in miniaturization, energy efficiency, and high-performance systems across industries.
Core Mechanisms Behind High Magnetic Performance
The performance of NdFeB magnets is rooted in the Nd₂Fe₁₄B tetragonal crystal structure, which combines several key magnetic phenomena:
High Saturation Magnetization (Js):
Iron’s 3d electrons and neodymium’s 4f electrons (via RKKY interaction) generate a combined spontaneous magnetization of 1.61 T, a record among rare-earth intermetallics.
Strong Uniaxial Anisotropy (Ku):
The crystal’s c-axis exhibits Ku = 4.6 MJ/m³, stabilizing magnetic orientation and supporting coercivity values up to 2 MA/m (25 kOe) when alloyed with Dy or Tb.
Curie Temperature (Tc):
Native Nd₂Fe₁₄B has a Tc of 312°C. For high-temperature applications, additions like 3% Dy improve coercivity but lower Tc to around 200°C, a necessary trade-off.
Manufacturing Breakthroughs: From Powder to Performance
Two major manufacturing techniques enable broad industrial adoption:
Sintered NdFeB Magnets
Process: Jet milling (3–5 μm), die compaction, followed by liquid-phase sintering at 1050–1100°C.
Advantages: Delivers the highest (BH)max values—up to 512 kJ/m³ (64 MGOe)—allowing up to 95% size reduction in motors compared to ferrite magnets.
Challenges: Nd-rich grain boundaries are prone to corrosion; thus, surface coatings (e.g., AlN, NiCuNi) are essential.
Bonded NdFeB Magnets
Process: Injection molding of magnet powder with thermoplastic binders (epoxy or nylon).
Advantages: Allows complex shapes, tailored magnetization profiles, and lower tooling costs.
Typical Applications: Used in micro-motors, smartphone haptics, and radially oriented rotors for BLDC motors.
Sector-Wide Impacts: From Tesla to Turbines
Electric Vehicles (EVs):
A Tesla Model 3 traction motor contains ~1 kg of NdFeB magnets, enabling a 300 kW/kg power density—3x higher than traditional induction motors.
Projected to consume 45% of global NdFeB output by 2030.
New Dy-free technologies like grain boundary diffusion aim to reduce dependence on heavy rare earths.
Wind Turbines:
10 MW offshore direct-drive turbines use up to 2 tons of NdFeB, offering 98% efficiency, compared to 95% in geared systems.
Heavy rare-earth-free compositions (e.g., Ce-substituted magnets) are being developed to reduce cost and improve sustainability.
Consumer Electronics:
AirPods Pro integrate 0.1 g NdFeB magnets per earbud to achieve a compact design and powerful sound output.
HDDs utilize NdFeB in VCM actuators to deliver 24,000 TPI, supporting future 20 TB per platter storage capacities.
Environmental & Geopolitical Dimensions
Recycling Needs:
Less than 1% of NdFeB magnets are recycled today.
Emerging methods like hydrogen decrepitation and solvent extraction are achieving >95% recovery from end-of-life electronics.
Supply Chain Security:
China controls ~90% of global NdFeB production.
Strategic investments in refining outside China (e.g., MP Materials’ Mountain Pass, USA) are gaining traction.
Sustainability Impact:
Life-cycle studies show NdFeB magnets in EVs save ~15 tons of CO₂ over a vehicle’s lifespan vs. combustion engines—even after factoring in rare-earth mining emissions.
Future Horizons: Pushing Beyond Limits
Nanocomposite Magnets:
Nd₂Fe₁₄B/α-Fe multilayers could reach (BH)max = 1 MJ/m³, leveraging exchange-spring coupling for next-gen motors.
Additive Manufacturing:
3D printing of anisotropic NdFeB magnets offers 20% higher motor efficiency and the potential for embedded sensor applications in aerospace.
Spintronics Integration:
NdFeB thin films show promise in skyrmion-based data storage, with projections of 100 Tb/in² areal densities.