NdFeB Magnet Sintering Process
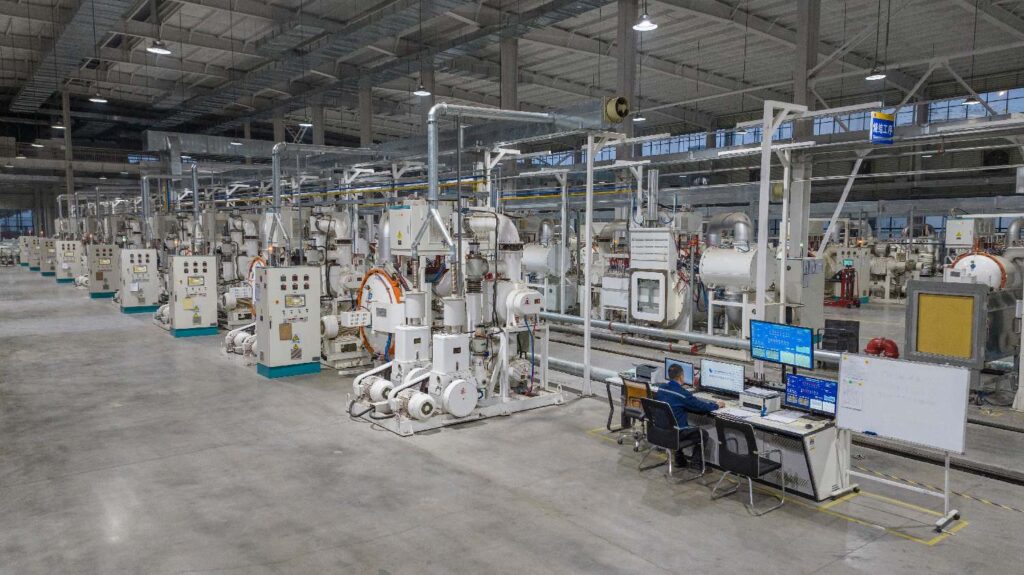
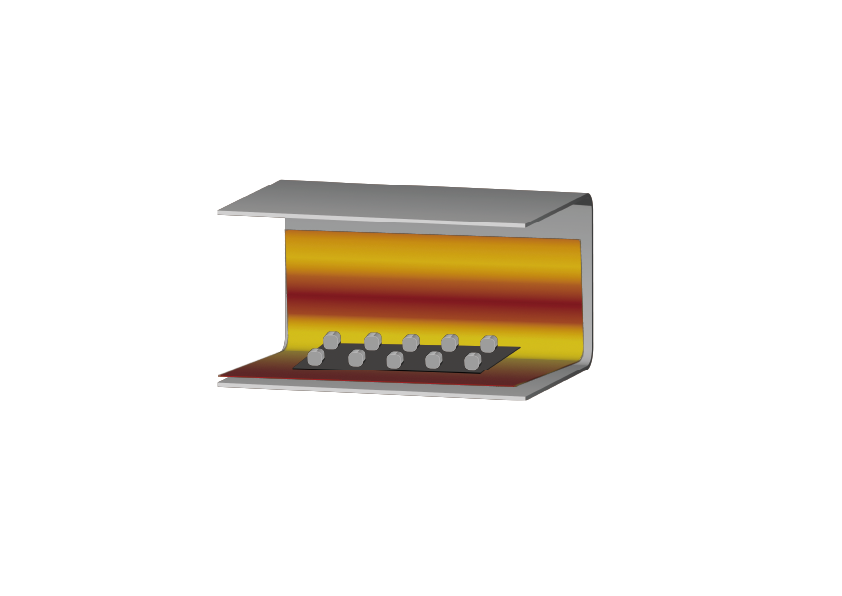
NdFeB Blocks Sintering Process
The sintering process of NdFeB magnets is a critical thermal treatment that transforms compacted powder into high-performance permanent magnets. Conducted under vacuum or inert gas atmosphere, this process consists of four key stages: First, debinding at 300-600°C to gradually remove organic lubricants and adsorbed gases; Second, liquid phase formation at 600-900°C where Nd-rich phases melt to facilitate particle rearrangement and pore filling; Third, densification at 1000-1100°C where Nd₂Fe₁₄B grains achieve consolidation through diffusion and liquid phase sintering; Finally, rapid quenching to preserve the optimized microstructure. Precise control of heating rate (typically 1-5°C/min), soaking time (1-4 hours), and cooling rate (50-100°C/min) is essential, as any parameter deviation significantly impacts the final density, grain size, and magnetic properties.
Technical Challenges and Innovative Solutions
The sintering process faces several technical challenges: Maintaining oxygen content below 100ppm to prevent neodymium oxidation; Balancing the competing requirements of densification and grain growth control; Ensuring microstructural homogeneity. Modern sintering technologies have developed multiple innovative solutions: Two-step sintering first achieves densification at 1050-1080°C followed by prolonged soaking at 900-950°C to suppress grain growth; Low-temperature sintering techniques utilizing Nd-Cu or Nd-Al eutectic additives enable processing below 950°C; Magnetic field-assisted sintering applies 1-2T fields during high-temperature stages to enhance grain alignment. These advancements not only improve magnetic performance (achieving coercivity exceeding 20kOe) but also significantly reduce energy consumption and production costs, making NdFeB magnets better suited for demanding applications like EV traction motors and wind turbine generators.
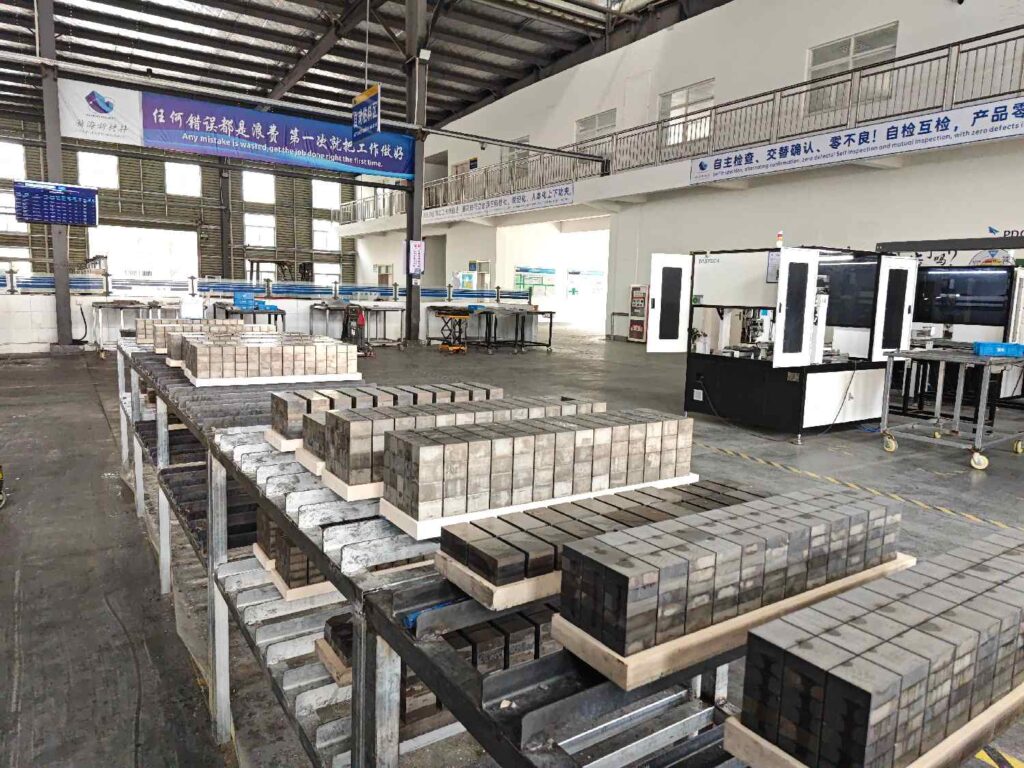